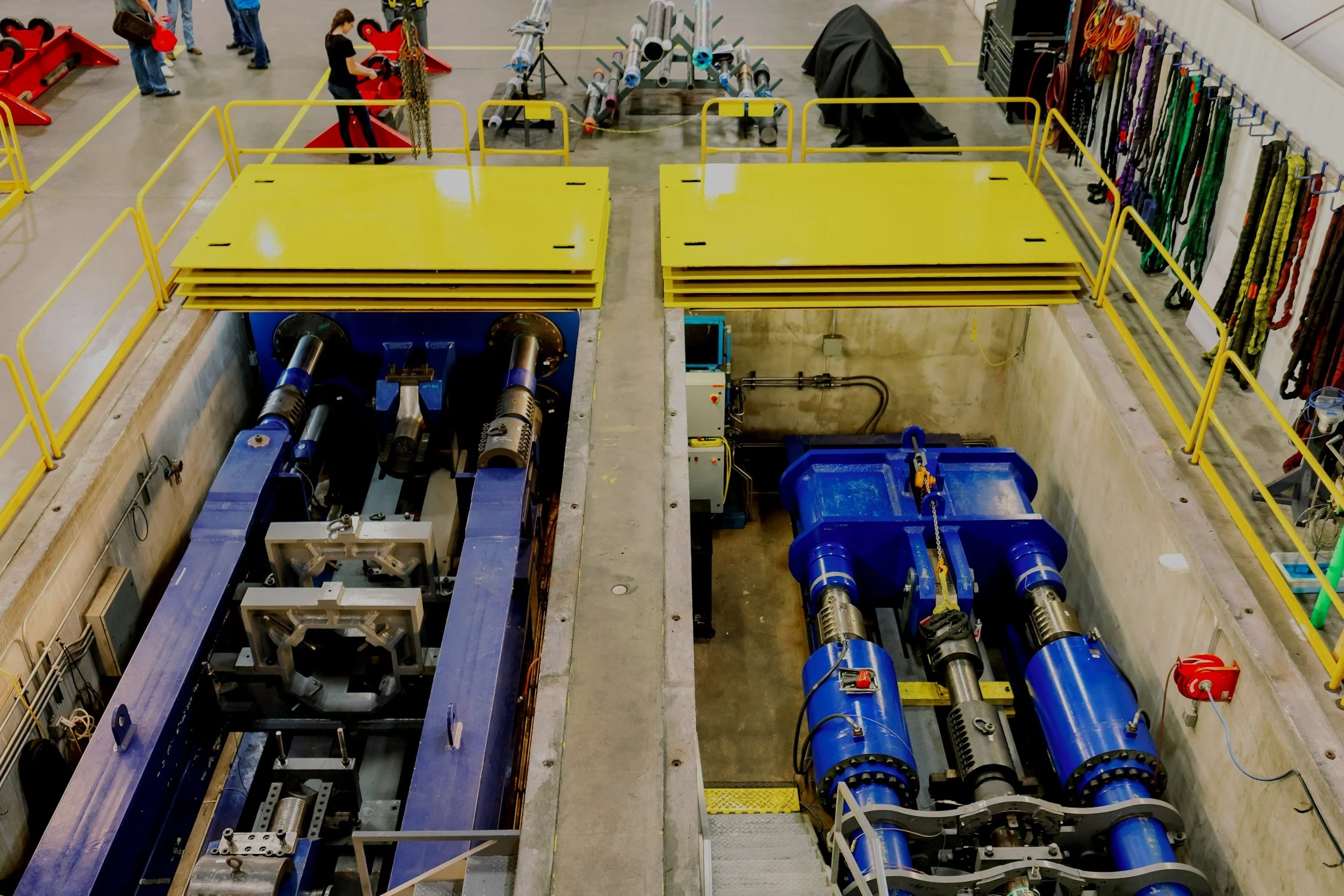
Our Capabilities
Our state-of-the-art facility offers the expertise and competence for full-scale testing.
What are the top 5 reasons to test?
Demonstrate product compliance with legal or regulatory requirements
Demonstrate product conformance to end-user or industry standard requirements
Gather information for the prediction of product operating life (time or operating cycles)
Determine absolute failure limits and mode(s) of failure
Validate manufacturers claimed performance limits
Testing can be conducted to API, ISO, ASME, ASTM, ANSI, AWEA, other industry standards, and customer specified protocols. Full-scale testing of wind turbine, nuclear, and other industrial components can also be accommodated and verified for conditional environments.
Get an in-depth look at our testing services and capabilities.

Load Testing
We provide a full range of load testing and by combining a variety of load testing including tension, compression, bending and pressure, we provide both standard and custom testing options for your assemblies and systems.
Tension
We provide a range of tension tests to a maximum tension capacity of 5,000,000 lbs. – Assembly or system test – full scale - max stroke 24”.
Bending
Our bend testing is widely used for systems, assemblies or components. Our bending maximum is 450,000 ft-lbs. (depending on length – max length 222”).
Compression
We provide a range of compression tests to a maximum compression capacity of 5,000,000 lbs. max stroke 24”.
Pressure
Our equipment ensures we can complete pressure tests – internal or external testing with liquid or gas.
Internal – liquid maximum 60,000 psi
Internal – gas maximum 45,000 psi
External – liquid or gas maximum 30,000 psi
Load Frame Descriptions and Capabilities
We have six load frames from 1.5 million lb. to 5 million lb.
Temperature
We provide a full range of high and low temperature testing.
• High temperature tests: 1200°F/650°C +
• Low temperature tests: -50°F
Torque
We have make and break power tong and bucking systems that have up to 150,000-foot pounds of torque testing capacity that can accommodate both vertical and horizontal configurations and tubulars up to 24 inches.
Fatigue
We perform multiple fatigue methods to replicate different environments such as high cycle (HCF)/resonant fatigue and low cycle (LCF) fatigue.
Flow
We have a 2,500 sq. ft outside area specifically designed to accommodate downhole tool and production equipment testing. This includes a 40-foot cased hole that we can suspend downhole tool assemblies for a variety of ISO, API and customer specified testing.
10 and 4 Channel System
High Pressure High Temperature
• For operations that are HPHT including aerospace, geothermal, oil and gas or industrial, we provide testing to 60,000 psi and 1200°F.
Pressure and Thermal Cycling
• Our three-stage centralized gas pressure system minimizes pressure-up time.
• When we combine pressure and thermal cycling with time, we incorporate our patented control software and automation.
Test Lab Safety Features
We have numerous safety features in our test labs to ensure the safety of our staff and your equipment including alarms, halts, and fail safes (control side).
Shielding
• In-ground test pits and cased holes capable of lengths up to 80 ft
• Underground bunker test frames are securely sealed with I-beam steel plates
Remote Monitoring
The automated sequential test loads are managed and monitored from secure control rooms.
• Real time test monitoring of images and data can be sent to any location globally via secure live streaming
• Remotely controlled HD cameras monitor with achievable video
Patented Control Software and Automation
Our patented control software offers automated sequential testing in a secure environment.
• Software provides simulated field applications
• High-speed data acquisition
• Controls load, bending, pressure, and temperature
• Intelligent load control
Strain Gage
MTS lays hundreds of strain gages a year for challenging applications and environments in our state-of-the art test lab and in field locations.
Uniaxial, Biaxial, and Triaxial strain gage configurations with various epoxy applications for maximum adhesion.